General Comments and Suggestions for Tubing pipe
Tubing Pipe must be Careful selecting, specifying, purchasing, and handling of tubing are essential to the successful use of tube fittings. Several general rules apply :
1. Metal tubing must always be softer than the fitting material. For example, stainless steel tubing should never be use with brass fittings.
2. When tubing and fitting are made of the same material, the tubing must be fully annealing. Mechanical, structural, or grade tubing should never be use for fluid systems.
3. Extremely soft or pliable tubing such as Tygon orunplasticized PVC tubing should always use an insert. Seals on the outside diameter of tubing require a certain amount of tube resistance for tight sealing.
4. Extremes of wall thickness should be check against our suggest minimum and maximum wall thickness. A wall too thick cannot be properly deform by ferrule action. A wall too thin will collapse under ferrule action and may not resist enough to allow the ferrule to coin out surface defects.
5. Tubing surface finish is very important to proper sealing. Tubing which is deeply embossed (such as copper water tube); has a visible weld seam on its outside diameter; or has flat spots, scratches, or draw marks may not seal properly when use with a fitting sealing on the tubing OD.
6. Oval tubing which will not easily fit into fitting nuts, ferrule, and bodies should never be force into the fitting. Such force tube entry will scrape the tube OD surface at the maximum diameter, making sealing difficult.
7. Laminated or multi-wall tubing, such as braided hose, should generally not be use with tube fittings. Since the fitting seals on the tube OD, system fluid may leak between hose or tube layers, causing “ballooning” and possible wall rupture.
Tubing Pipe for Gas Service
Tubing Pipe can apply in Gas services. Gases such as air, hydrogen, helium and nitrogen have very small molecules which can escape through even the most minute leak path.
Some surface defects on the tubing can provide such a leak path.
As the tube OD increases, the likehood of scratches or other surface defects also increases.
The most successful connection for gas service will occur if all installation instructions are carefully follow and the heavier wall thickness of tubing are select from the Tables.
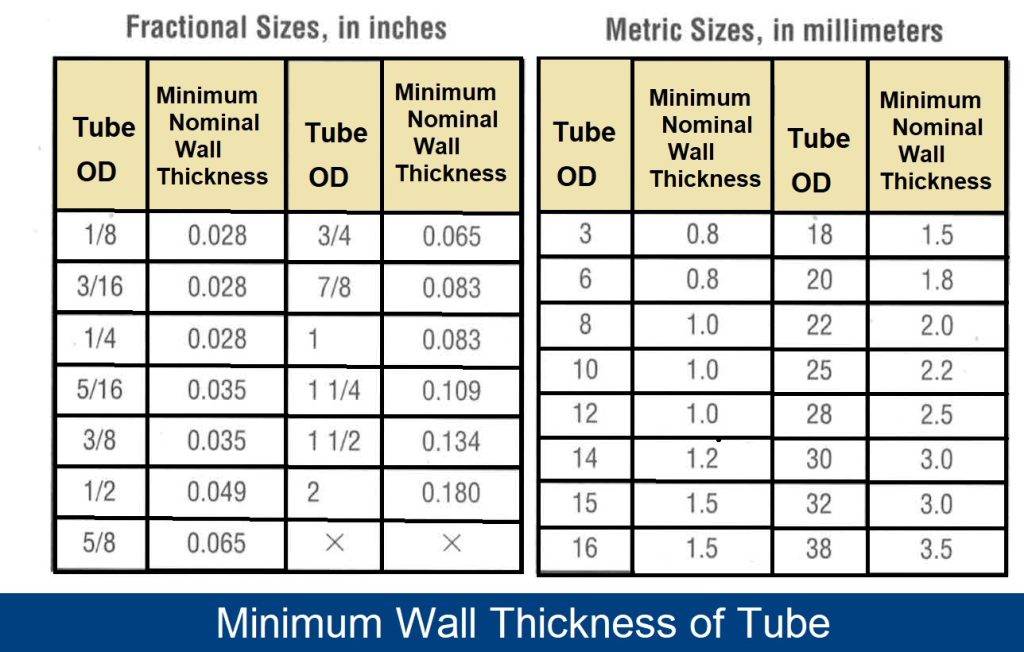
A heavy wall Tubing Pipe resists ferrule action more than a thin wall tube and allows the ferrule to coin out minor surface imperfections. A thin wall tube will collapse. Therefore it offers little resistance to ferrule action during pull-up and reduces the chance of coining out surface defects, such as scratches.
For the greatest safety factor against surface defects in any gas system, use a wall thickness no less than the following : Fractional Sizes, in inches Metric Sizes, in millimeters.
Tubing Pipe Selection and Specification
When using a tube fitting combine with Tubing it is important to remember that the built-in fitting quality will be greatly compromise by the use of poor quality tubing.
Tubing should always be considere as the fifth important component, since the first four pieces nut, back ferrule, front ferrule, and body all come to you fully inspect and assemble.
It is short-sight to purchase a high quality fitting and use it with the cheapest tubing available.
Although buying tubing to ASTM or equivalent specifications is a start towards tubing quality, it is only that-a start. Most such specifications allow rather wide latitudes in several important factors.
For example ASTM A269, a very commonly use stainless steel tube specification, refers one to A450 General Requirements which include:
Straightness and Finish
Finish tubes shall be reasonably straight and have smooth ends free of burrs. They shall have a workmanlike finish. Surface imperfections (Note 1) may be remove by grinding, provide that a smooth curve surface is maintain, and the wall thickness is not decrease to less than that permitt by this or the product specification. The outside diameter at the point of grinding may be reduce by the amount so remove.”
Note 1-An imperfection is any discontinuity or irregularity found in the tube.
What is a “workmanlike” finish? How deep or how flat must the grinding be?
ASTM A269 also allows OVALITY of the tube to be 2× the OD
tolerance of ±0.005 in., or ±0.010 in. for thin-wall tube. If this ovality were to really be, for example, ±0.010 in. (0.510 in. by 0.490 in. for 1/2 in. OD tubing) the tube would not even fit into most tube fittings.
So the mere use of ASTM specifications does not really mean that you have a quality piece of tubing. Tubing quality depends on the integrity and the quality consciousness of the tubing supplier.
To be sure of selecting tubing whose quality is good enough to perform properly with the precision-made tube fitting, we suggest that the following variables be consider:
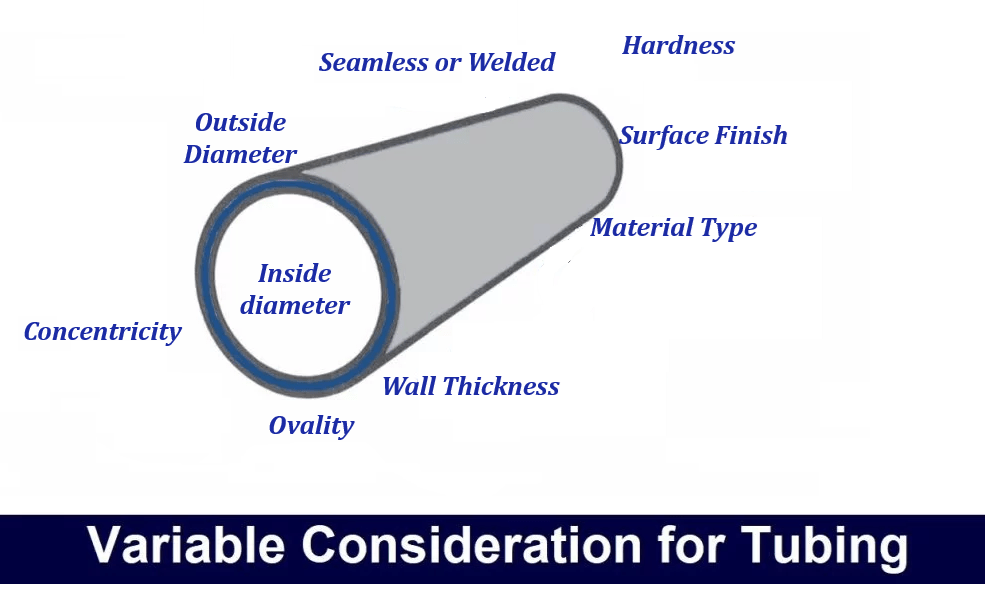
- Material and method of manufacture
- Wall thickness and outside diameter
- Surface finish
- Hardness
- Concentricity
- Ovality
The limits well be considerably than permitted in ASTM specifications
Often a user can specify certain limits on a tubing purchase order, particularly on large purchases, at no extra cost. These limits may well be considerably narrower than those permitt in ASTM specifications.
For example:
Restricted OD Tolerances-Typical ASTM tubing specificationsshown on p. 2-12 permit various plus and minus tolerances. Some users will not accept tubing with a “minus” tolerance because it is more difficult to seal undersize tubing. Also for tubing 1/8 in. OD and smaller, we suggest restriction to ±0.003. in.
Restricted Surface Finish Tolerances-As mention above, ASTM specifications are ambiguous and unclear on the subject of finishes. In particular, when stainless steel welded and drawn tubing is specifie, poor quality of weld or weld bead removal can cause sealing problems when the tube and tube fitting are assemble.
Poor welding usually results in a visible depression, which ferrules cannot seal. Poor weld bead removal results in a raise portion or in a flat spot at the weld. Any of these conditions may result in a leak when made up into flareless tube fittings.
A good rule of thumb, sometimes written into weld tube specifications, is:
“External weld bead shall not be visible to the naked eye.” You can always see the weld when you look at the tube inside diameter.
Then inspect the OD at that location. You will not be able to see the weld on the OD if it is high quality tubing.
Hardness Restrictions-All flareless tube fittings require that the tubing be softer than the fitting material. Various terms are used to describe tubing hardness. In general, metal tubing should be fully annealed to work properly with tube fittings. While most stainless steel tubing is restricted to a maximum Rockwell Hardness of 90 HRB, many users specify that this hardness be further restricted to 80 HRB. Such tubing lowers installed cost because it is more easily bent and installed. Although stainless steel tube fittings may be used on stainless steel tubing with a hardness of 90 HRB maximum, we suggest that, whenever possible, you specify a maximum hardness of 80 HRB.