Pressure Regulator
Definitions Pressure Regulator
Pressure regulator is a control valve that reduces the input pressure of a fluid to a desired value at its output. When the medium conditions for inlet pressure and medium flow change, the regulator can still maintain a stable outlet pressure and flow within a certain range.
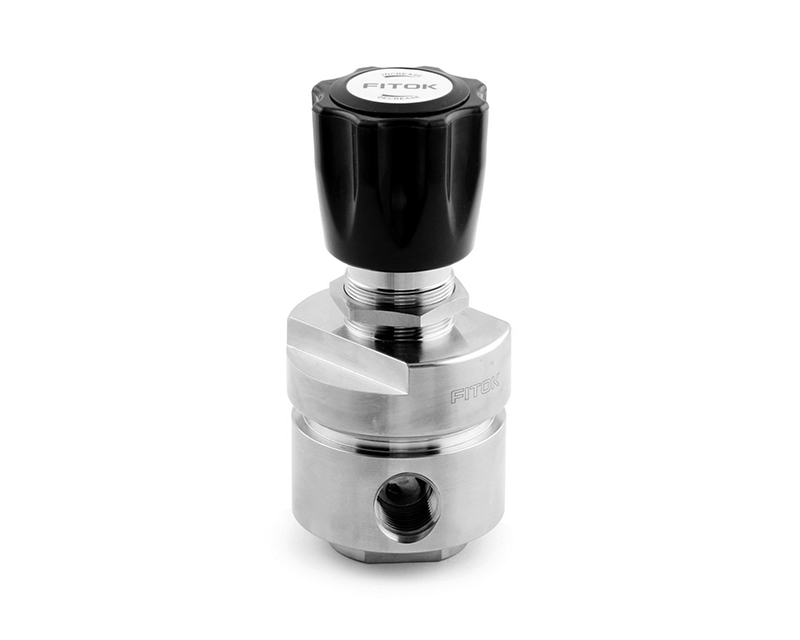
Major Components
- Loading element
- Sensing element
- Control element
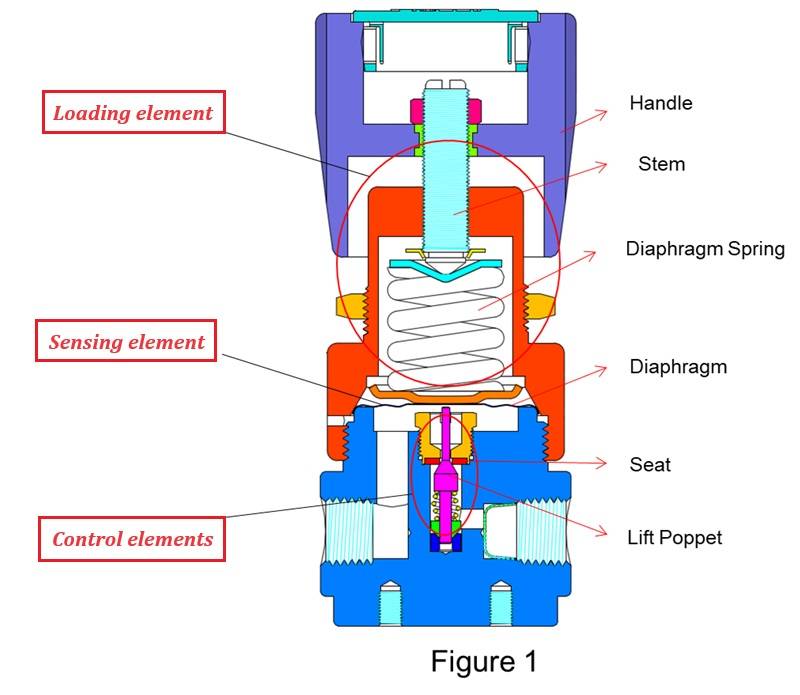
Element Pressure Regulator:
Loading element Pressure Regulator :
Used for the operator to set the outlet pressure of the regulator by applying a loading force. Mainly the handle, valve stem, range spring.
Sensing element:
By sensing the pressure changes in outlet chamber to balance the loading force and the outlet pressure, and physically connect the loading element and the control element.
Types: diaphragm (Figure 1) or piston.
Control elements:
Pressure Regulator the relatively high inlet pressure to low outlet pressure and adjust the orifice size through the stroke of the poppet to maintain a stable output pressure. The control elements mainly include the seat, seat retainer, poppet and poppet spring.
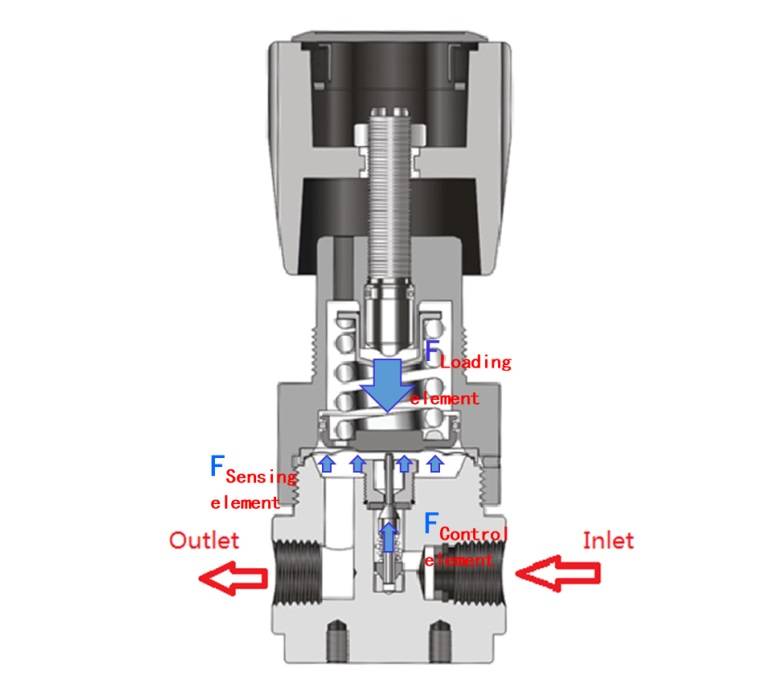
Working Principle Pressure Regulator
High pressure gas flows through a small orifice into a large space, causing the pressure to reduce. Pressure regulator is about balance of forces. The equation goes as follows:
Floading element= Fsensing element + Fcontrol element
Wherein:
Floading element= Diaphragm spring force (F1)
Fsensing element = Outlet pressure × diaphragm area(F2)
Fcontrol element= Inlet pressure× Poppet area (F3)+ Poppet spring force (F4)
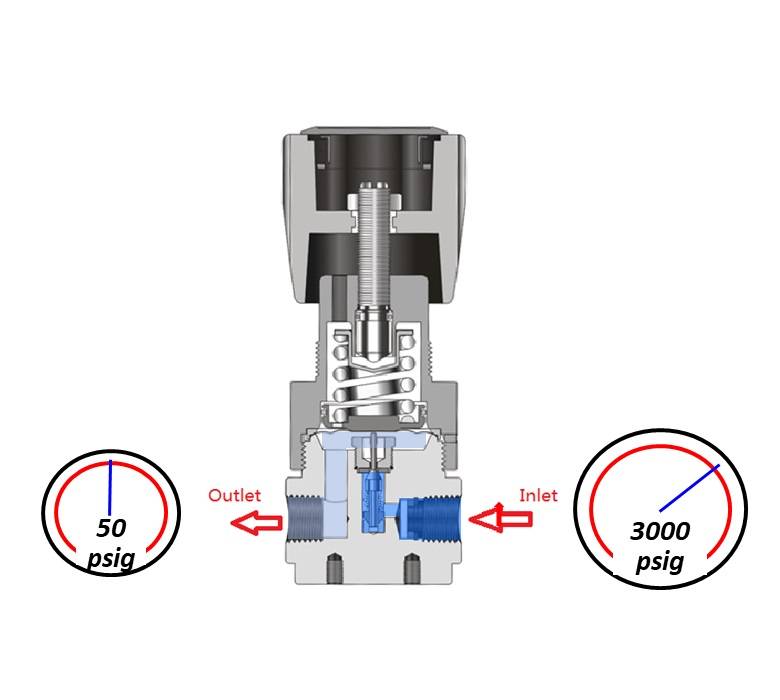
The upstream pressure falls from 3000 psig to 2500 psig as cylinder is depleted. The downstream pressure rises from 50 psig to 55 psig.
3000-2500=500
55-50=5
5/500=1%
The supply pressure effect (SPE) of the regulator is 1%.
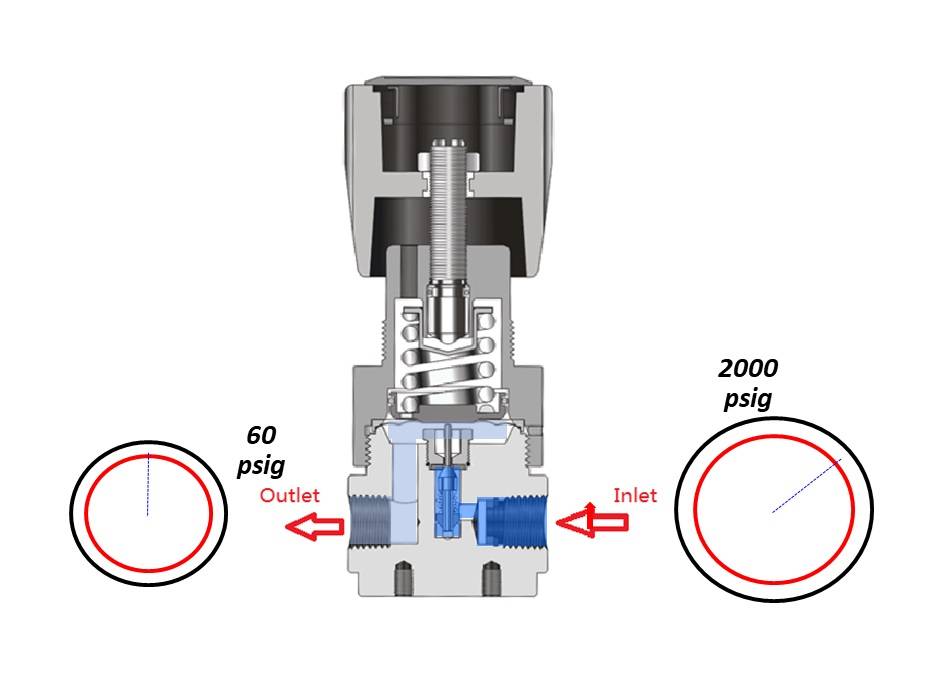
When the upstream pressure falls from 3000 psi to 2000 psi afterward the downstream pressure will rise by?
3000-2000=1000psig
1000×1%=10psig
50+10=60psig
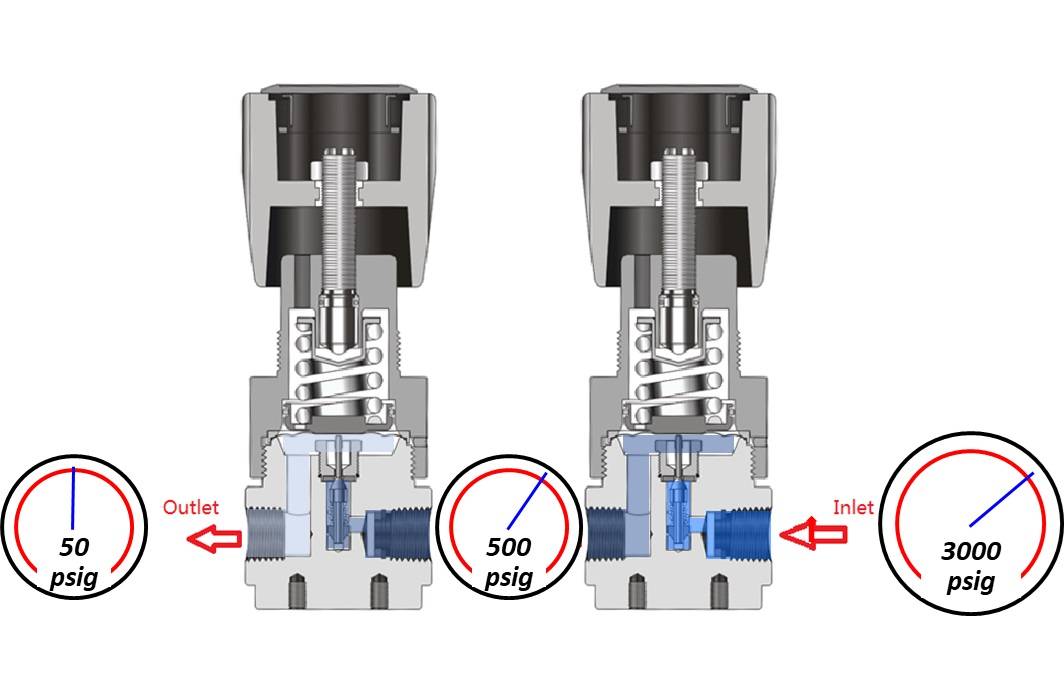
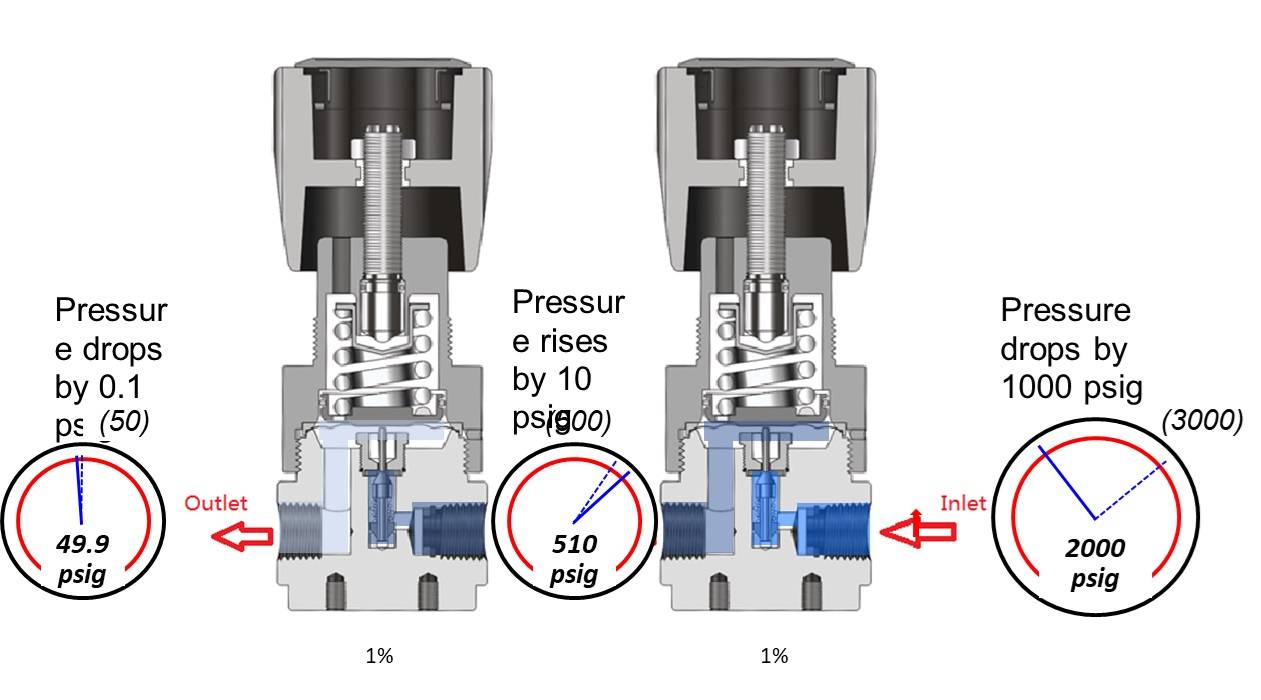
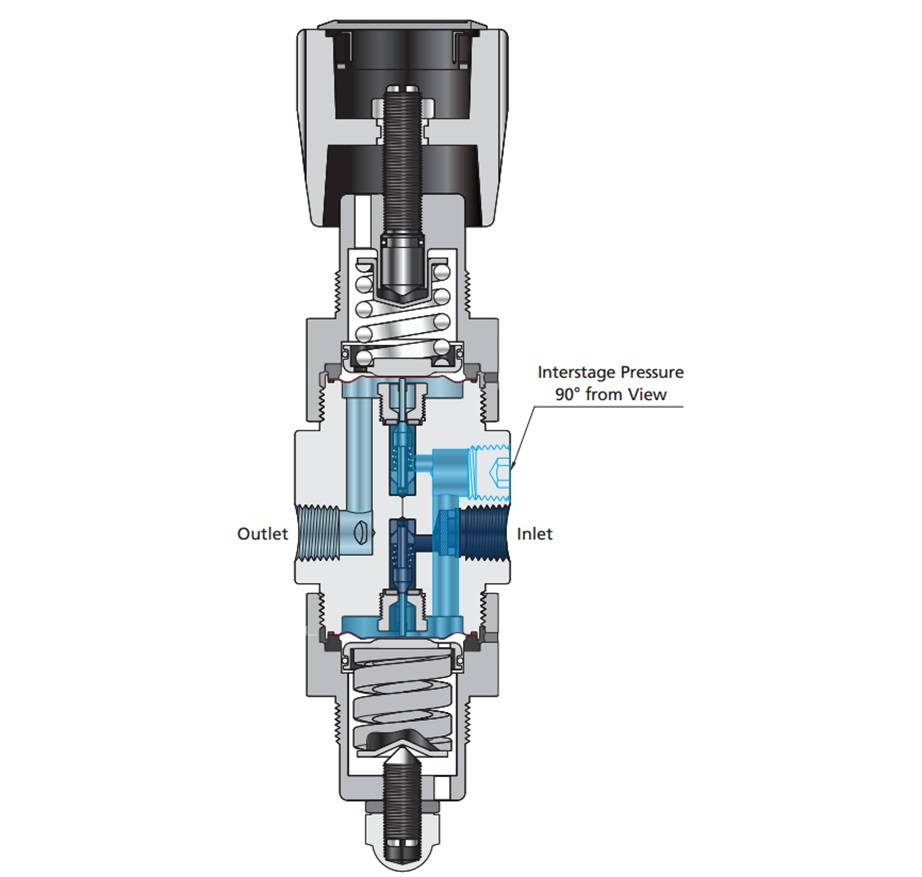
Two stage pressure regulators are two single stage regulators in one that operate to reduce the pressure regulator progressively in two stages instead of one. SPE is reduced to 1%×1%,as the application in FCR-1D.
When the inlet pressure falls to the first-stage outlet pressure, the first-stage regulator will remain open, and the SPE will recover back to 1%.
Working PrincipleFlash
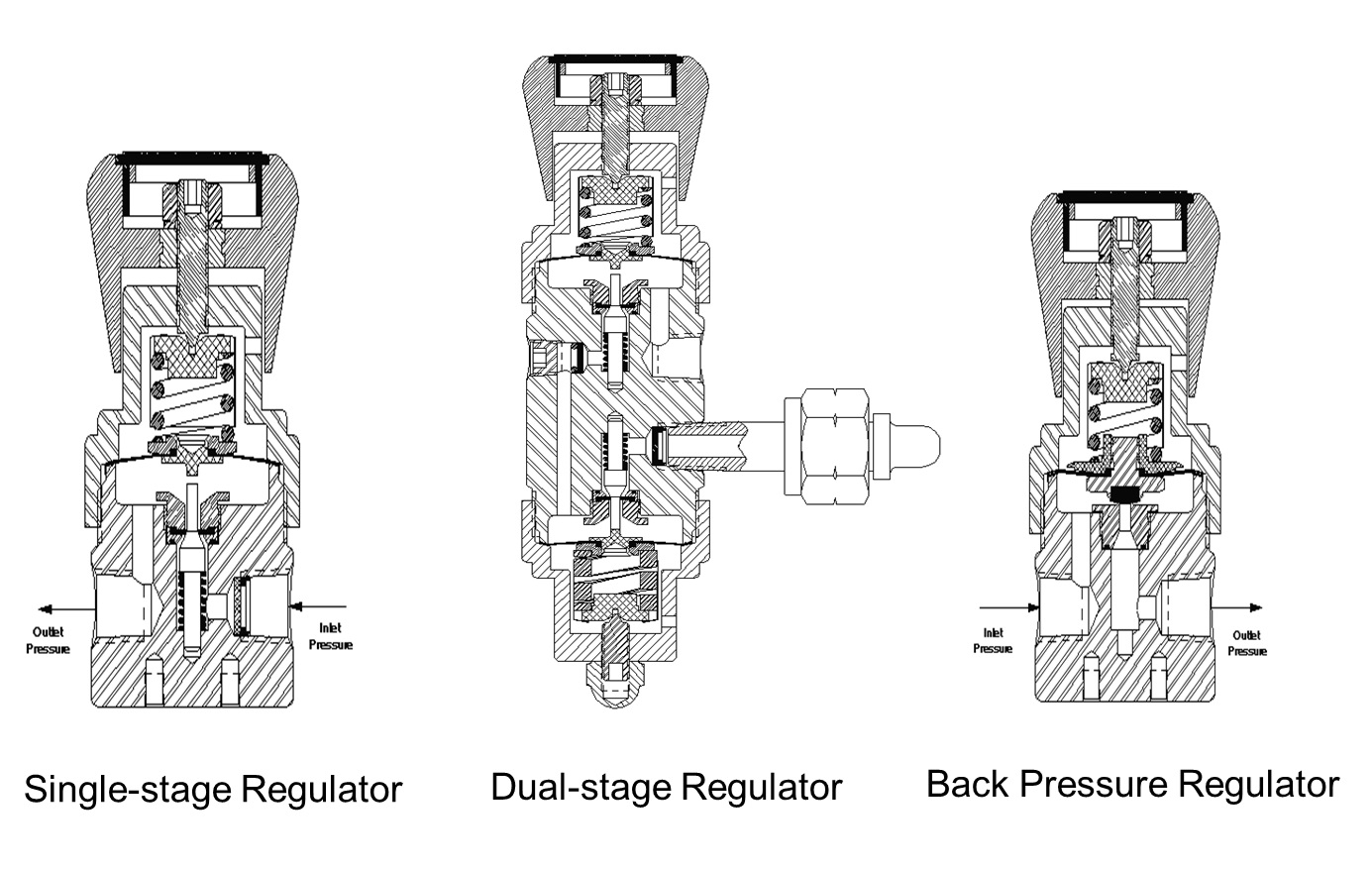
Types of loading elements pressure regulator
a. Spring loading (Figure 1)
As the most common types of loading, it is space-saving, convenient and cost effective; However, the increase of outlet flow will cause the pressure drop.
b. Pneumatic loading
Commonly used for high pressure application, and the ratio of pneumatic loading pressure to the outlet pressure is 7:1.
Types of sensing elements
a. Diaphragm sensing (Figure 1)
Greater sensitivity with large diaphragm areas and material choices of 316L, Elgiloy, Hastelloy C-22/C-276, Alloy X-750.
Advantages: Greater sensitivity and simplicity, suitable for ultra-high purity applications.
Disadvantages: Output pressure 500 psig max. and overpressure will cause the diaphragm rupture.
b. Piston sensing
High outlet pressure up to 10,000 psig and dynamic sealing achieved through the combination the piston and O-ring
Advantages: Constant sensing area for reliability
Disadvantages: Less sensitivity with O-ring sealing; not intended for ultra high purity application due to lubrication.
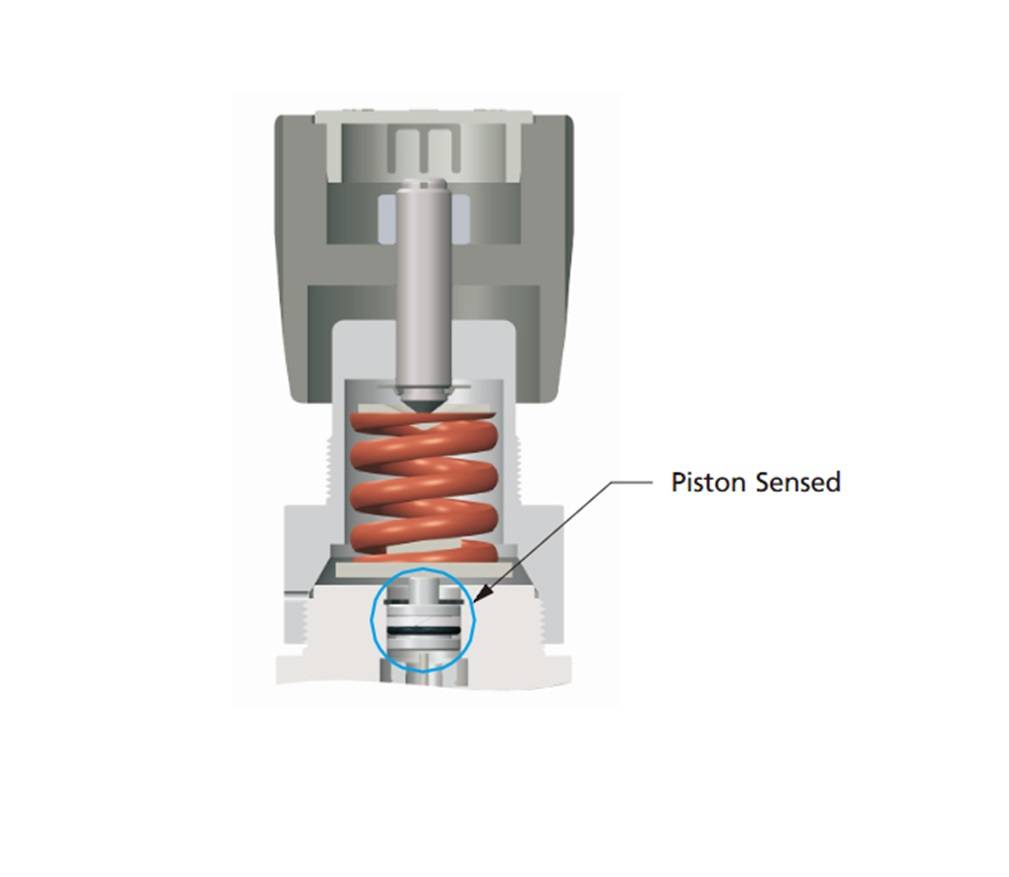
Types of control elements
a. Unbalanced poppet
For unbalanced poppet, poppet area is subject to influence of the inlet pressure.
- Advantages:
Inlet pressure provides additional force to enhance the engagement between the poppet and the seat
- Disadvantages:
When the inlet pressure falls, the outlet pressure rises. This often happens when steel cylinders are used as a source of gas. When the inlet pressure is high, the seat is subjected to a large force, requiring a hard seat.
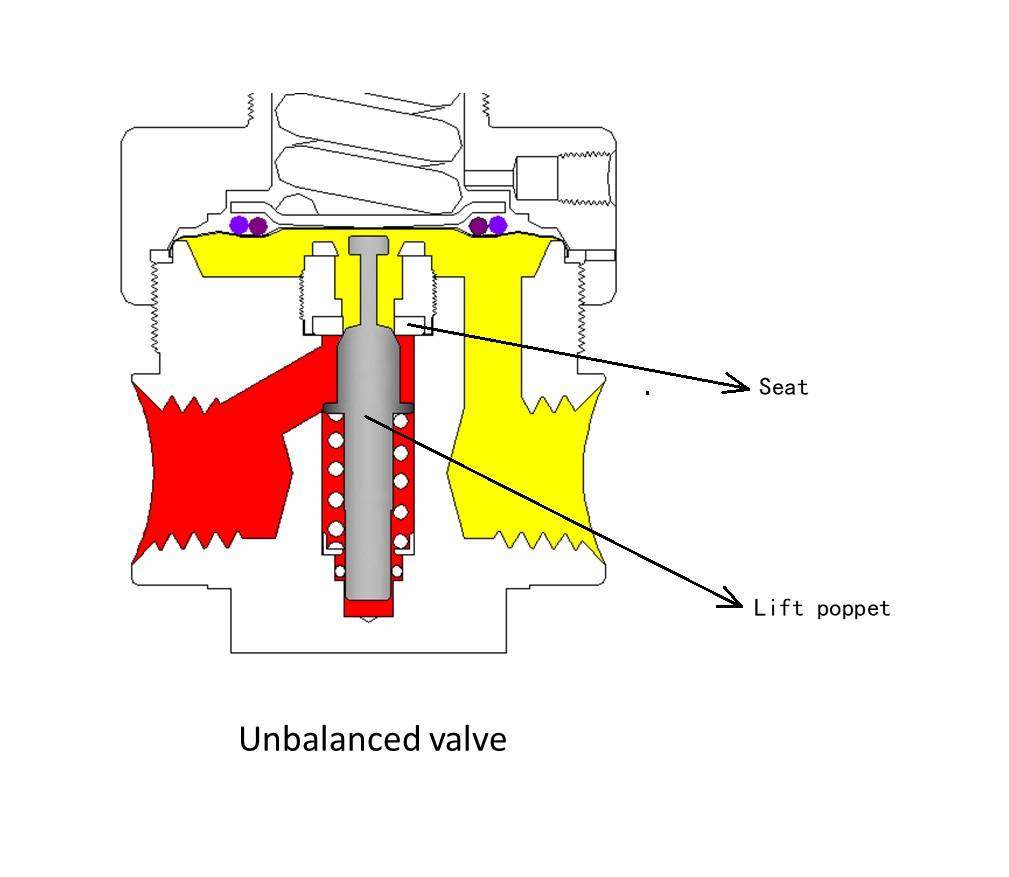
b. Balanced poppet
For balanced poppet, poppet area is almost unaffected by the inlet pressure
Advantages:
The poppet has a balance hole that connects the outlet chamber to the bottom of the valve body, reducing the poppet area which the inlet pressure acts on. When the inlet pressure falls, the outlet pressure rise is not significant.
Disadvantages:
The poppet has large diameter, which allows for large flow. But it is not suitable for small flow control, and needs higher cost.
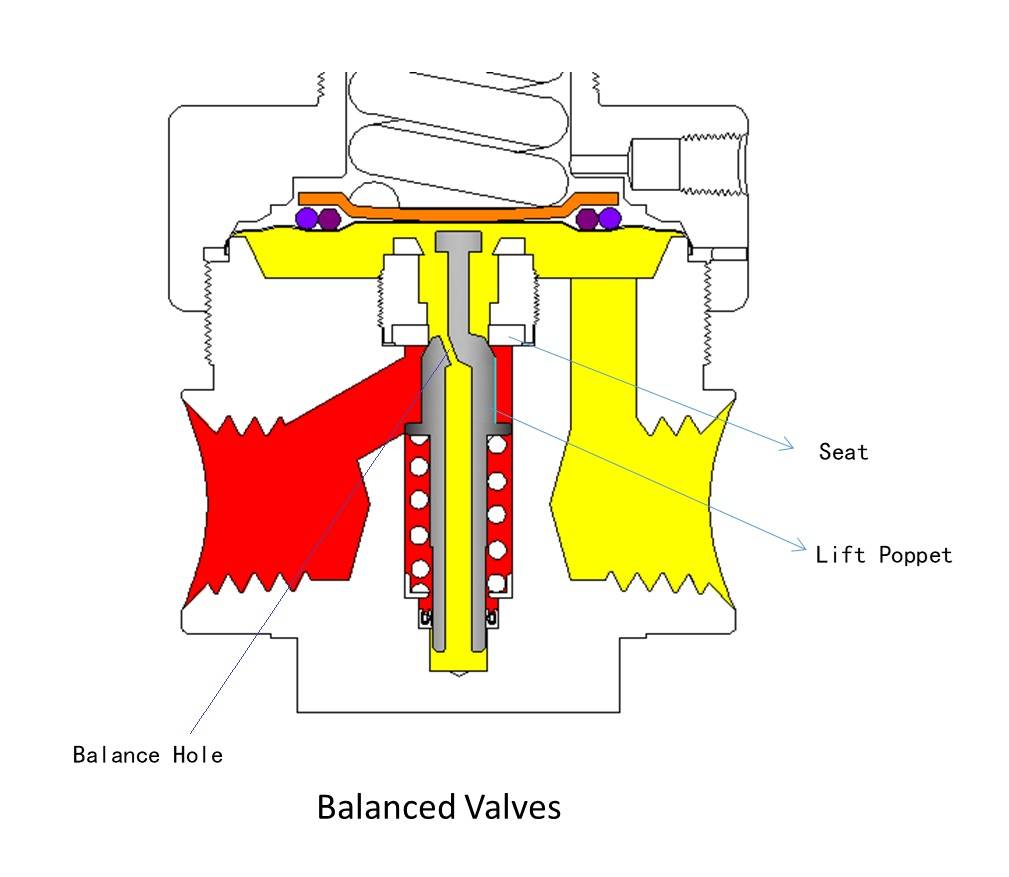